
But most linear guides also operate under static conditions for at least a part of their life. Linear bearings are primarily associated with motion-for example, moving a tool, dispensing head, or load from one point to another-hence, the focus on dynamic load capacity in sizing and selection. Exceeding the static load capacity will certainly (not just statistically) compromise bearing performance. If this deformation is exceeded, the running characteristics of the bearing will be degraded, resulting in vibration, noise, and increased friction.Īs its name suggests, static load capacity is applicable only in a static (non-moving) state, and although it’s not used in bearing life calculations, static load capacity is an important parameter for recirculating linear bearings.
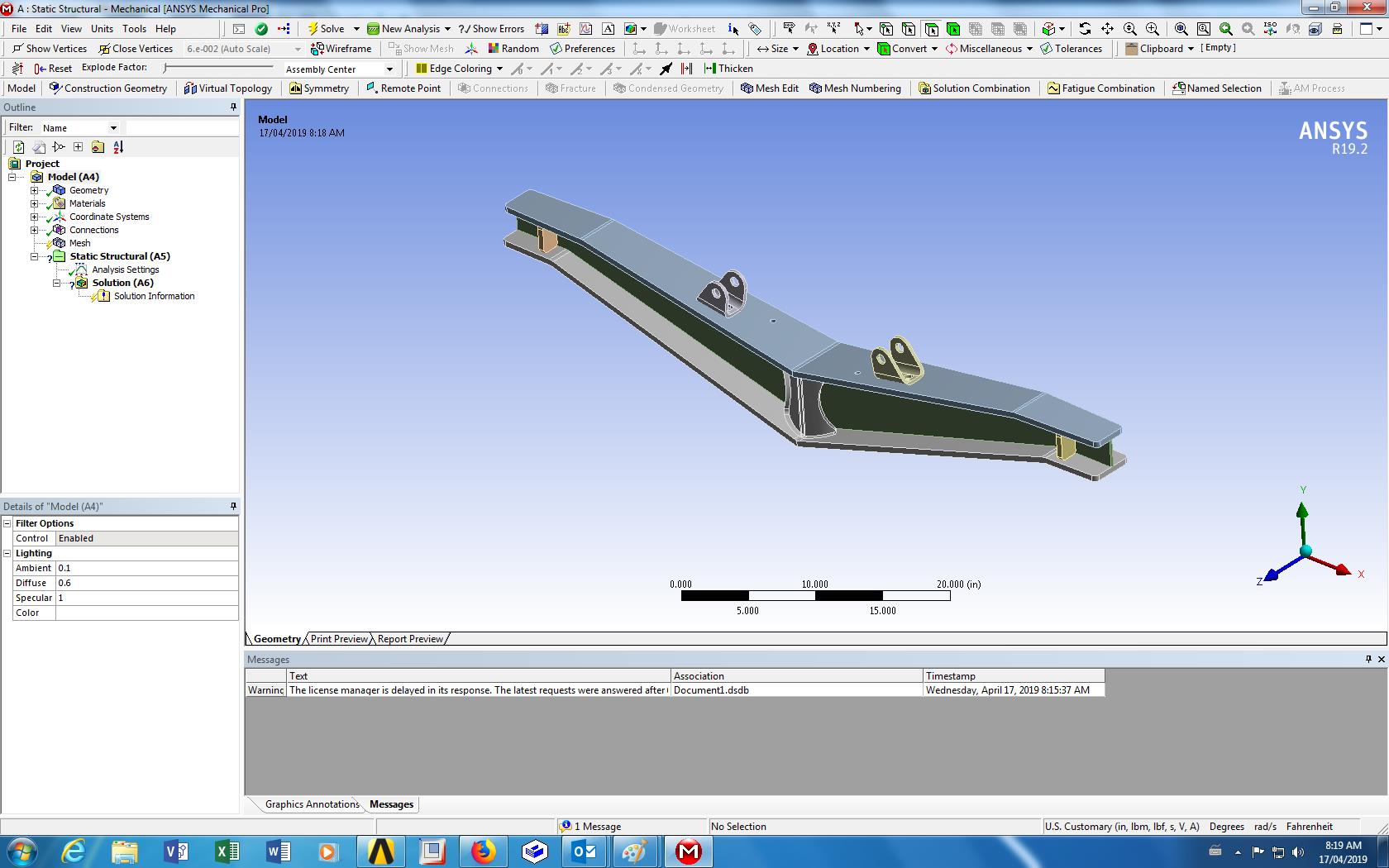
This is the load at which a linear recirculating bearing will, with 90 percent certainty, achieve the targeted service life before fatigue occurs. Static load capacity, on the other hand, is the force that causes permanent deformation of the rolling element (ball or roller) and raceway equaling 0.0001 times the rolling element diameter. Without that clarification, the fabrication shop tends to go to the extreme just to be safe, and proceed to follow the D1.1 criteria for cyclic structures, which will add additional fabrication time that most likely was not picked up during the estimating phase.When sizing a recirculating bearing, most designers and engineers focus on bearing life, which is based on dynamic load capacity. With that being said, a simple phone call to the EOR would clear it up. It should always be noted in the contract documents, and to take it a step further, any applicable notes should be added to the shop and field drawings, but I've never seen any of it done. and can determine whether a structure is static or cyclic, however, that is not 100% reliable because I'm not an engineer. I can usually look at the types of connections, welding, etc. On the other hand, cyclic loaded structures have movement due to impact, waves, wind gusts and strong earthquakes.
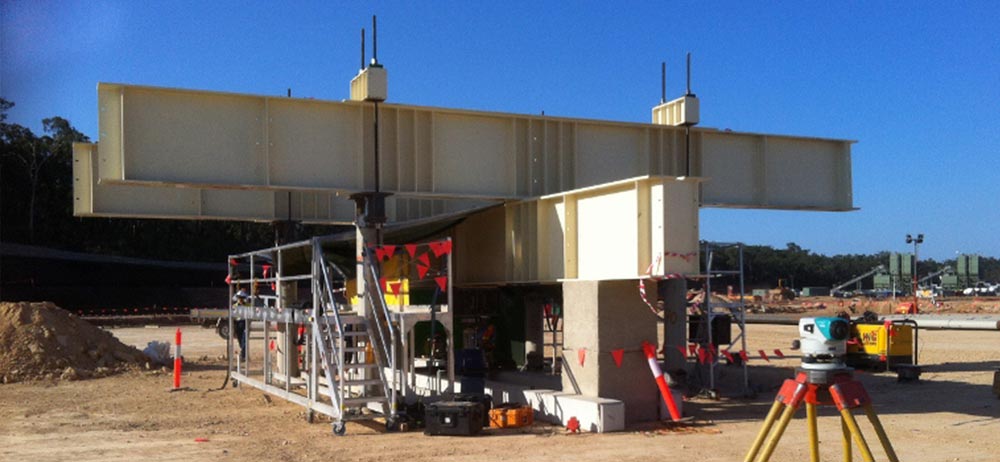
Static loads exhibit very little movement and have little or no change due to the balance and the equal action of the opposing forces in the structure. Where the girders are continuous over several piers or columns, the girder may experience complete load reversals, which increase the stress range used for fatigue analysis. The number of cycles needed before fatigue analysis is necessary is typically over 10,000 cycles where the stress range is the difference between the maximum and minimum loads. The people walking and working in the office represent a very small load that is typically neglected and lumped into the static load. Static loads do not change over time, or if they do, the change is slow and relatively infrequent. When a truck goes across the bridge, the bridge experiences a load several times greater than it did for the car. Every time a car crosses the bridge span, the girders and deck experience a load. Think of cars and trucks rumbling over a bridge span as examples of cyclic loads. Cyclic loads are loads that fluctuate over time. Therefore, when there is a question on the nature of the loads, ask the designer.

That information is not typically transferred to the detail fabrication or erection drawings. The structural design drawing will often include the nature of the loads at the connections so the fabricator/detailer has the information needed to detail the connection.
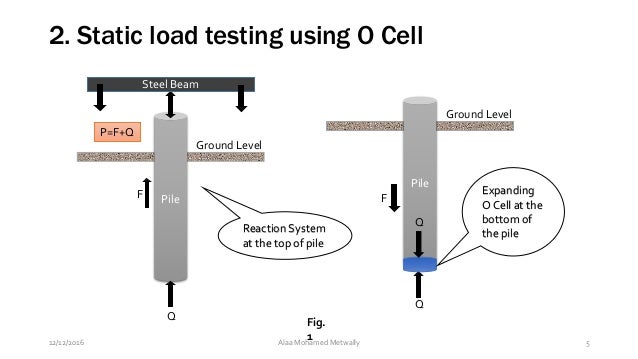
The engineer or designer should be consulted.
